Gasoline direct injection, how it works and why we need it. The GDI type of fuel delivery system is one of the latest waves in fuel management deployed on new model vehicles. This technology is what many car designers believe can help them achieve demanding corporate average fuel economy numbers while reducing tailpipe emissions and greenhouse gasses.
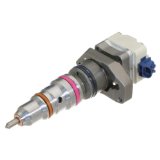
Direct Injector
Recently it was in the news that average fuel economy will be 54.5 miles per gallon by the year 2025. Each time the C.A.F.E. goes up car makers respond by pushing their fuel injection technology to the next level. In the 80s car makers abandoned the carburetor for
fuel injection systems.
The first type to come on the scene was called throttle body injected and where more like a carburetor then the modern fuel injection systems. As emissions standards got tighter car-makers developed Port technology that was much more efficient. Gasoline direct injection takes this to a new level.
GDI is not new technology
Direct injection has been around for many years on diesel engines. With this type of fuel delivery the gasoline is injected directly into the combustion chamber. To do this specially designed injectors shoot the fuel into the high pressures and extremely high temperatures that exists as the cylinder comes up to be fired.
Expert Auto Repair Tip: Take it from someone who knows...Having the
online repair manual is a life-saver when it comes to DIY auto repair and maintenance. Whether you are working on a
Ford,
BMW,
Dodge, or something more exotic; we probably have the manual you need.
To prevent the heat from igniting the fuel in the line these injectors are designed to quickly and completely seal after the fuel is sprayed. They must also be able to spray with pinpoint accuracy at these increased pressures. If this did not happen the fuel would not enter the cylinder or overcome the compression that was building in the combustion chamber.
Advantage of injecting gas direct
The direct injection fuel delivery system allows for very lean operation at cruising speeds. When operating under heavy loads the GDI can provide the needed increase in the air fuel mixture by means of high speed computer controls that are now available at much lower prices. Being able to run at such a lean ratio at cruising speed or highway conditions can increase fuel economy on average by as much as 40% while decreasing emission levels.
Spraying the fuel directly into the cylinder also increases the volumetric efficiency because the intake manifold only delivers air to all cylinders. In the past with multi port, vortec or CPI (central port injected) the air and fuel was mixed in the intake manifold and swirled as it entered the combustion chamber. With GDI it can be injected on demand as needed.
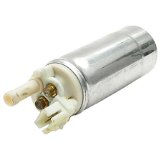
Fuel Pump
One of the more interesting things about a direct injection fuel delivery system is the fuel pressure itself. It is highly pressurized typically between 500 and 1500 PSI when it is sprayed into the cylinders. Just 20 years ago when automobiles still used carburetors the fuel system was only pressurized to about 6 PSI. When F.I. came on the scene they bumped it up to about 35 PSI.
The 1500 pounds per square inch that is used in the direct injection delivery system is similar to the pressures that diesel engines use. Under this massive pressure the fuel charge arrives as a vapor. The injectors release a relatively small perfectly shaped spray of fuel around the sparkplug just before it ignites. This means only the area around the sparkplug has air and fuel to trigger combustion.
For more information about diagnosing problems with cars visit the online auto repair homepage. For more of the latest automotive technology articles like this one visit the blog for diy car repair.